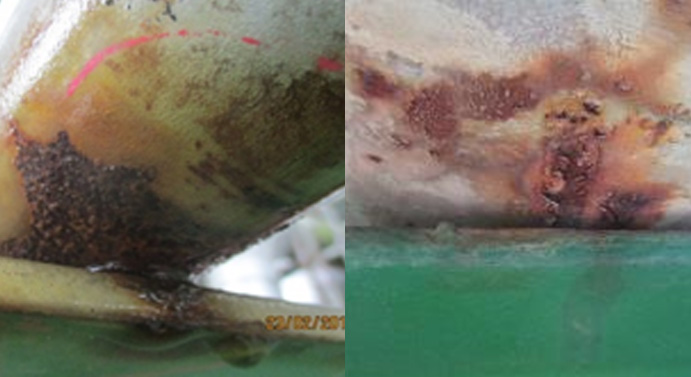
Case Study
Corrosion Under Support (CUS) Management in Aging Facilities Using Innovative Online Inspection and Restoration Method: Safer, Lower Cost, and Higher Accuracy
Figure 1 – Corrosion under support
Figure 2 – CUS inspection device: a) Innovative pipe lifting device, and b) Ultrasonic Thickness Measurement (UTM) probe
CLIENTS:
Petrochemicals & Refining Processes
SERVICE:
CUS (Corrosion Under Support) Management: Online Inspection, Integrity Assessment, Online Lifetime Recovery
The Situation
Corrosion Under Support (CUS) is one of many chronic corrosion problems faced by petrochemical and refining industries. Leak of hydrocarbon and hazardous chemicals impacts safety, environment, and production in many of our clients’ production plants. Additionally, cost of replacement is significantly high because production needs to be fully stopped, isolated, and cleaned prior to repair. For instance, one of our case studies shows that the total cost of repair can be up to 30,000 USD per CUS point. Therefore, CUS management is crucial for maintaining safety, production, and reliability. There are 3 key factors for solving this chronic problem:
1) Root cause analysis, 2) Inspection technology, and 3) Restoration technique.
Root cause of CUS problems is mainly associated with moisture that is trapped in between pipe without pipe shoe, and beam, deteriorating the paint around that area. Figure 1 shows CUS after the paint has been deteriorated by the moisture trapped between the pipe and beam. Additionally, thermal expansion and shrinkage of pipes from temperature difference during day and night accelerates paint wearing. In general, pipes, which are exposed to high moisture environment for over 15 years, are classified as high risk.
Radiography Testing (RT) is unpractical in this case to examine the remaining thickness due to insufficient space and angle for the installation of radiography source and recording films. As a result, the result from RT is difficult to accurately interpret. Although new technologies such as Electromagnetic Acoustic Transducer (EMAT) and Short Range Ultrasonic Test (SRUT) have been introduced in the inspection service market, our experience using these technologies reveals that accuracy is not sufficient to assist or determine critical actions.
There might be many restoration techniques available in the service market such as wear resistant coatings, or composite wrapping. However, thesesolution may not be appropriate in this situation.
CUS is one of the most difficult problems to solve due to the available working space and the integrity of corroded pipes limit most of the current inspection and restoration methods.
Our Approach
The best approach to solve CUS problem starts from obtaining the remaining thickness at a CUS area through direct measurement. The direct measurement in this approach means the pipe must be lifted up from the beam until the gap between the pipe and the beam is accessible for performing Ultrasonic Thickness Measurement (UTM) then measure the remaining thickness of the corroded area directly.
However, in order to do so, the existing pipe integrity is important as pipes require sufficient strength to resist the bending stress from lifting, in other words, the generated stress must not be over the yield strength. Therefore, the existing pipe integrity is evaluated prior to lifting to ensure that the process will not damage the corroded pipes.
Site survey to observe CUS is performed by our specialist to estimate CUS risk level. Based on our experience in observing over 30,000 CUS points, we can statistically estimate the initial damage depth of CUS categorized into level 0, 1, 2, and 3 according to customer site environment and pipe characteristics.
Next, REPCO NEX’s innovative pipe lifting device (as shown in Figure 2a) is utilized to carefully lift the corroded pipe. One of the main features of this device is it can monitor the stress generated on the pipe in real time. As a result, the pipe stress condition can be controlled within the safety range throughout the lifting and inspection period. After that a direct measurement is performed by using a UTM probe as shown in Figure 2b.
Finally, a special wear resistant coating is applied on the corroded pipe of which the wall loss is less than 1 mm. In the case that the corrosion is more than 1 mm, composite wrapping is recommended for restoration. The life time of pipes from our CUS repair and recovery method is evaluated to be more than 15 years based on our accelerated tests in laboratory and experience.
Value Delivered
- Proactively 100% prevent leak from corrosion under support (CUS)
- Reduce cost of inspection and repair/recovery about 10 time compared to original client practice
- Predict CUS life time and plan for recovery within 5 years
- Cost optimization and budgeting plan
- Estimate 15 years lifetime plus after our recovery/restoration
- Reduce customer project management time about 30% by providing one stop service. All related tasks for CUS recovery are included in our scope (strategy, survey, inspection, scaffolding, repair, monitoring)