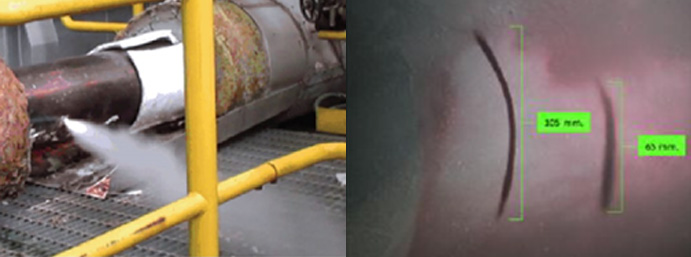
Case Study
Root Cause Analysis and Problem Solving of Steam Leakage at a Cracking Furnace
Figure 1 – Superheated steam leakage
Figure 2 – On-site investigation
Figure 3 – Failure analysis: a) cross-sectional analysis, and b) optical microscopy
Figure 4 – Example of tree diagram for root cause analysis
Figure 5 – Simulation-assisted root cause analysis: a) simulated damage, and b) actual damage
Figure 6 – Simulation of water injection: a) water injected into the desuperheater line, b) water is being evaporated, and c) remaining water droplets are impacting the desuperheater line
CLIENTS:
Petrochemicals, Refinery, Chemical Processing, and Power Generation.
SERVICE:
Reliability Improvement
The Situation
From 1999 to 2017, furnace process reliability and furnace mechanical reliability issues were accounted for furnace breakdowns or slowdowns resulting in the ethylene production loss of 0.4% and 0.5% respectively [1]. These issues can be stemmed from various reasons such as upset conditions, human errors, corrosion-erosion, equipment aging, or even improper mechanical design.
In this case study, the furnace was shut down due to superheated steam leakage from the desuperheater line located outside the firebox as shown in Figure 1. This leakage negatively impacted not only ethylene and steam production but also compromises human safety. Normally, the superheated steam from the cracking furnace unit is used in driving the turbine of the main compressor, the heart of an ethylene plant. Therefore, in some scenarios, decrease of steam production may lead to plant slowdown resulting in uptime loss. The temperature of the superheated steam at this point is normally over 500°C, and this excessive temperature hindered the online leak sealing team in stopping the leakage.
Therefore, for this kind of problem, finding the root causes is much more difficult than finding the failure mechanisms because everything is in an enclosure. Consequently, identifying the correct preventive actions to prevent the recurrent case is inevitably difficult.
Our Approach
REPCO NEX tackled this problem by conducting an on-site investigation. The Penetrant Test (PT) shows that the damages or cracks started from the inner pipe surface as shown in Figure 2. Then, a part of the desuperheater line was cut and removed from the site for further failure analysis at a laboratory. The results from failure analysis using methods such as Cross-Sectional Analysis (Figure 3a) and Optical Microscopy (Figure 3b) emphasize that the cracks were initiated from the inner surface and were impacted by cyclic loads.
Next, the tree diagram given in Figure 4 was used in the root cause analysis, and the results from on-site investigation and failure analysis helped the investigation team scope down the possible root causes. After scoping down, one of the root causes was improper water atomization due to abnormalities of the desuperheater nozzle. To verify this root cause, advanced engineering tools such as engineering simulation was necessary.
In order to affirm that the simulation results can be used in the analysis, the simulation model must be validated first. In this case study, the simulation model was validated by comparing the simulated damage (Figure 5a) with the actual damage (Figure 5b). The simulated damage (Figure 5a) is almost identical to Figure 5b, the actual damage. Therefore, the simulation results can be used in further analysis.
According to the simulation results, the water injected into the desuperheater line could not properly evaporate prior to impacting the inner pipe surface. As a result, the water droplets led to thermal cyclic loads and initiated the cracks. This phenomenon is illustrated from Figure 6a through Figure 6c.
Finally, the preventive actions following by inspection program to monitor the conditions of the desuperheater line and the desuperheater nozzle were provided to the client in order to avoid the recurrent case. These preventive actions and inspection program were also applied with client’s other furnaces, and the client has not had the recurrent case since applying the preventive action and the inspection program in 2015.
In conclusion, REPCO NEX provide a one-stop reliability improvement service. This service includes: 1) On-Site Investigation, 2) Failure Analysis, 3) Root Cause Analysis, and 4) Simulation-Assisted Root Cause Analysis and Problem Solving. REPCO NEX have a special team with strong experiences in various fields to solve all challenging cases.
Value Delivered
- Ensure that all assets continue to safe operation.
- Able to optimize PM plan.
- Able to prevent Low Probability of Failure.
- Know when each parts are likely to fail.
- Know the gap for improvement.
References
- C. L. Cagnolatti, "Top Seven Causes for Lost Olefin Production," Hydrocarbon Processing, vol. 94, pp. 31-36, April 2015.
- Solomon Associates, "Worldwide Olefin Plant Performance Analysis," 2017.