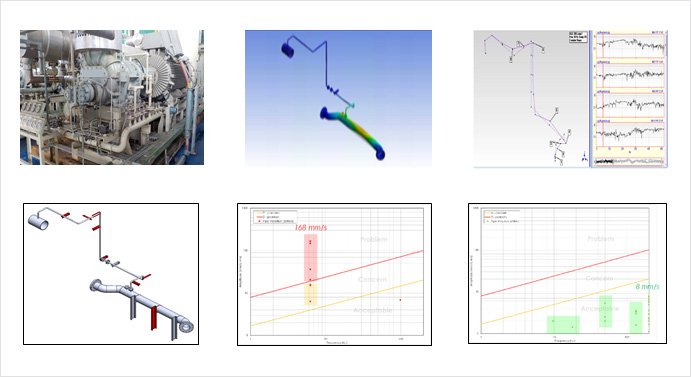
Case Study
The Elimination of Vibration Problem by Synchronizing Advanced Vibration Diagnostic and Finite Element Analysis
CLIENT:
Petrochemicals Plant
Objective:
Vibration Problem Solving, Mitigation and Elimination
Many vibration problems in the petrochemical industry have been solved over the past decade such as problems related to structure support, pressure vessel, and compressor. Vibration diagnosis can identify the causes of vibration, such as looseness, imbalance or misalignment, leading to the identification and execution of proper solutions. The problems, however, become more complicated when the vibration is resulted from resonance of the structure. The most common way to solve this problem is through trial and error approach, resulting in a time consuming and less than cost-effective method.
In many instances, the impact of vibration problems not only result in suspending production but also impact the environment. For example, a chemical substance leakage due to vibration failure and can become exposed to the environment, and consequently the company can incur more loss from being prosecuted by the law.
Our Approach
Utilizing an advanced vibration analysis with Computer-Aided Engineering (CAE), Finite Element Analysis (FEA) and Computational Fluid Dynamics (CFD) enables the diagnosis to have a higher efficiency in solving the vibration problems and the three main approaches are Modal, Harmonic, and Transient Dynamic Analysis using high performance software and high-performance computing.
A thorough understanding of vibration data and simulation techniques becomes powerful tools used to identify and mitigate vibration issues by implementing the effective solutions, including
- Mitigates piping resonance
- Mitigates rotating equipment resonance (Agitator, Pump, Blower Motor)
- Mitigates static equipment resonance (Pressure Vessel, Tank, Heat Exchanger)
- Eliminates vortex shedding vibration
- Eliminates flow induce vibration (FIV)
- Prevents rotor dynamics vibration
- Analyzes vibration fatigue and remaining asset life assessment
Value Delivery
The simulation result leads us to see the dynamic characteristics of the vibration, hence it serves as a guidance in solving the vibration problem at the root cause. Typically, the solutions for solving resonance usually visualize only change of stiffness and mass of the system that shifts from natural frequency by at least 15%; however, our simulation service provides further. The conceptual design and fabrication drawing are delivered to clients and ensure that problems could be solved by using our one stop service.
In the case of force vibration such as vortex shedding and flow-induced vibration, the solution is considered with structure modification, redesign, and additional support in operating adjustment.
Rotor dynamics design is applied to any kind of turbomachine and the proper design can prevent high vibration during operation at a high speed.
Vibration is a cyclic load hence fatigue occurs simultaneously. The simulation result provides an assessment on the remaining life, which is useful for designing a maintenance plan.
After the vibration problem has been solved and the vibration magnitude is acceptable as the criteria. The client gains the benefit in term of increased production capacity, reduced mechanical downtime and uptime loss, and increased asset reliability and availability.