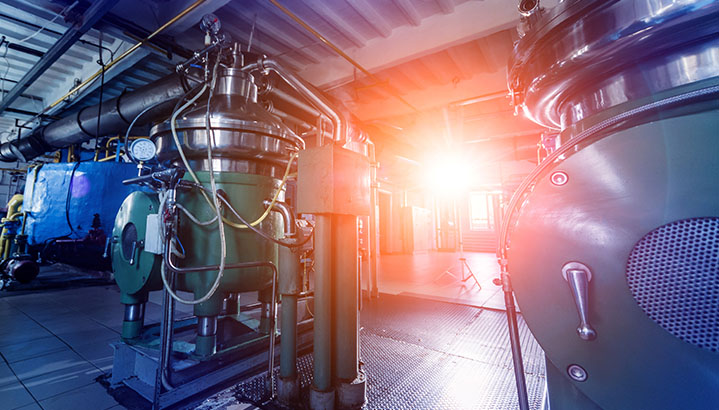
REPCO NEX Vibration Solution provides vibration troubleshooting covering various rotating equipment types including piping and structure systems. Our unique innovation for bearing fault detection in extremely low-speed machines (SRoDTex: Slow Rotation Diagnostic Technology) can solve industrial pain points through early detection to enhance reliability and inspection effectiveness. We provide one-stop service for vibration solutions by our experienced practitioner with certified vibration analyst category IV and hands-on advanced engineering experience of more than 30 years. REPCO NEX is the confidential solution provider and partner in the special vibration field for your company.
Our Service
- Vibration Measurement and Analysis
- Advanced Machinery - Diagnostic
- Piping and Structure Vibration Analysis
Our Product
- Low-Speed Machine Fault Detection by SRoDTex System
WHY REPCO NEX FOR VIBRATION SOLUTION?
"World-class competency with over 30 years experienced practitioner from more than 30 plants."
More than 20,000 reference cases in various rotating machine types including piping and structural system saving over 100 MB per year.
Produced unique innovation solution (REPCO NEX's patent) e.g. SRoDTex (Slow Rotation Diagnostic Technology) for bearing fault detection in extremely low-speed machines.
Analysis by certified machine diagnostic analysts (Vibration Category IV).
Know-how of advanced engineering for problem-solving and analysis of any rotating machine including high-power steam turbine, multi-stage centrifugal compressor, reciprocating compressor, large and extremely low-speed rotary dryer machine, and pump or cooling tower unit.
OUR VIBRATION SOLUTION PACKAGES
PACKAGE 1 VIBRATION MEASUREMENT AND ANALYSIS
WHY REPCO NEX
Expert
- On-site vibration measurement by skilled workmanship for accurate vibration data collection
- Vibration and Root Cause Analysis (RCA) performed by our experts (Certified Vibration Specialists, Turbo-machinery Specialist, API, etc.)
One-Stop-Service
- REPCO NEX can provide one-stop service including Machine Monitoring System (MMS) strategy, inspection test plan, on-site vibration measurement, root cause analysis, simulation, recommendation, and repairing.
BENEFITS
Fault Diagnostic Report
Useful vibration measurement data assists to manage machine conditions for maintenance and operation based on international standards and REPCO NEX machine failure library of real cases for accurate fault diagnostic and excellent maintenance skills.
Digital Platform Embed
Automated fault diagnostic has been developed from the knowledge of in-house experts with 30 years of experience and more than 20,000 reference cases to ensure the accuracy in machine diagnostic and provide a prompt online report system.
Machine Monitoring System (MMS) Strategy Implementation and Gap Analysis
Provide a suitable Machine Monitoring System (MMS) strategy and filled the gap to improve machine inspection effectiveness.
PACKAGE 2 ADVANCED MACHINERY DIAGNOSTIC
WHY REPCO NEX
Expert
- Root Cause Analysis performed by experts (Certified Highest Machine Diagnostic analyst (CAT4), Turbo-Machinery specialist, API, etc.)
Experience
- REPCO NEX achieves solving complex machinery including high-power steam turbine, multi-stage centrifugal compressor, reciprocating compressor. (>1,500 cases)
Advanced Measurement Tools
- Special measurement and analysis techniques to model dynamic behavior and Operating Defection Shape (ODS) for integrated machinery assessment and monitoring.
BENEFITS
Accurate Fault Diagnostic
- Historical operation and vibration data analysis benchmarking to international standard and REPCO NEX best practices database with failure library.
- On-site investigation and provide practical solutions.
Prevent Unplanned Breakdown
- Keep productivity by estimating machine conditions before failure to schedule a maintenance plan.
24/7 Remoted Monitoring Service
- Provide distant monitoring and diagnostics services to ensure machine health and productivity
PACKAGE 3 SRoDTex (Slow Rotation Diagnostic Technology)
BENEFITS of SRoDTex
- 6 months of early detectability since the initial phase of defect for sufficient managing operation and maintenance plan.
- Bearing failure in early-stage detection for low-speed machine.
- Reduced opportunity losses from the unplanned breakdown.
- Proven 200 units with SRoDTex for low-speed machines in chemical plants.
FEATURES
- Innovative patented sensor with signal processing effective for low-speed machine fault detection. (<600 rpm)
- Early installation without any machine modification..
- Approved hazardous area rated.
- Online software for web-based analysis.
- Mobile application for real-time monitoring.
SRoDTex Specification
Features | Specifications |
Machine Speed Range | 1 - 600 RPm |
Maximum Temperature | 120°C |
Rod Material | Noise Reducing Material |
Required Area for Installation | ⌀ 30 mm. |
Required Drill Holle for Installation | None |
Hazardous Area Rated | Yes |
PACKAGE 4 VIBRATION MEASUREMENT AND ANALYSIS
Many piping and structure damages are caused by high vibration issues since design or long continuous operation that leads to catastrophe from hazardous leakage.
WHY REPCO NEX
Expert
- Root Cause Analysis performed by experts (Certified Vibration Specialist, Piping Design, Corrosion Specialist, API, etc.)
Experience
- REPCO NEX achieve solving piping and structure system over 30 years in 30 plants experiences e.g. flow-induced vibration of C3 feed pipeline and new designed reboiler pipeline.
Advanced Measurement Tool
- Special measurement and analysis techniques to model dynamic behavior and Operating Defection Shape (ODS) for integrated piping and structure system.
One-Stop-Service
- REPCO NEX provides one-stop services including strategy, visual assessment, vibration analysis, simulation, engineering, and modification.
BENEFITS
Reactive Program
- Prevent unplanned shutdown from hazardous leakage lead to explosion from damaged piping.
- Identify sources of piping vibration problems with integrated assessment and propose effective solutions with finite-element analysis (FEA) to optimize vibration level and piping stress based on engineering practice.
Proactive Program
- Assisting to handle hidden vibration problems with a piping system and provide a professional assessment program that can reduce the risk and solve the problems completely.
- Optimizing inspection cost with the short-term program for piping vibration assessment program.
REPCO NEX Vibration Solution provides vibration troubleshooting covering various rotating equipment types including piping and structure systems. Our unique innovation for bearing fault detection in extremely low-speed machines (SRoDTex: Slow Rotation Diagnostic Technology) can solve industrial pain points through early detection to enhance reliability and inspection effectiveness. We provide one-stop service for vibration solutions by our experienced practitioner with certified vibration analyst category IV and hands-on advanced engineering experience of more than 30 years. REPCO NEX is the confidential solution provider and partner in the special vibration field for your company.
Our Service
- Vibration Measurement and Analysis
- Advanced Machinery - Diagnostic
- Piping and Structure Vibration Analysis
Our Product
- Low-Speed Machine Fault Detection by SRoDTex System
WHY REPCO NEX FOR VIBRATION SOLUTION?
"World-class competency with over 30 years experienced practitioner from more than 30 plants."
More than 20,000 reference cases in various rotating machine types including piping and structural system saving over 100 MB per year.
Produced unique innovation solution (REPCO NEX's patent) e.g. SRoDTex (Slow Rotation Diagnostic Technology) for bearing fault detection in extremely low-speed machines.
Analysis by certified machine diagnostic analysts (Vibration Category IV).
Know-how of advanced engineering for problem-solving and analysis of any rotating machine including high-power steam turbine, multi-stage centrifugal compressor, reciprocating compressor, large and extremely low-speed rotary dryer machine, and pump or cooling tower unit.